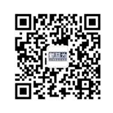
微信公眾號二維碼
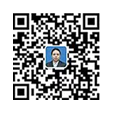
微信咨詢顧問二維碼
新益為5S咨詢公司概述:車間是以生產(chǎn)線為核心,以車間環(huán)境、人員等為內(nèi)容的空間。而精益管控下的車間則是通過緊抓車間核心、嚴控車間內(nèi)容來確保有效價值實現(xiàn)的物理場所。企業(yè)通過產(chǎn)品獲得收益,價值來源于產(chǎn)品,而產(chǎn)品來源于車間。因此,所有企業(yè)都應遵循一個基本原則:關注車間精益管理,確保車間活動都是能夠直接產(chǎn)生價值的活動。
車間精益管理
1、價值的源頭
福特不顧客戶價值需求而堅守T型車,使其付出了慘重的代價丟失了大量的市場份額;而通用汽車之所以能夠后來居上,恰恰是因其能夠迎合顧客價值需求的結(jié)果。事實表明,爭取客戶的關鍵就是從客戶的價值需求角度出發(fā),找到客戶真正需要的價值。下面這個例子更直觀地表現(xiàn)了客戶所需價值與產(chǎn)出者界定價值之間的斷層。
豐田汽車通過調(diào)查發(fā)現(xiàn),那些事業(yè)有成、地位卓著的成功人士通常不會考慮購買豐田汽車。因為當時,豐田汽車雖然具有高品質(zhì)、省油、經(jīng)濟等特點,但是完全不符合豪華汽車的特點。當時日本車間給公眾的印象就是實用、可靠,但絕非豪華車。為了打開豪華車市場,豐田進行了詳細的客戶調(diào)查。
豐田發(fā)現(xiàn),20世紀80年代豪華車車主在考慮購車時所考慮因素的重要順序如下:身份地位和高端形象,高品質(zhì),轉(zhuǎn)售價值,車的性能,安全性。可以看到,豪華車的客戶群最關注的車的特點是其高雅的外觀和優(yōu)越的品質(zhì)。了解到這些后,豐田的研發(fā)目標集中起來:擁有高貴典雅的外形,同時要想超越其他豪華車品牌比如奔馳,還必須擁有比它們更勝一籌的品質(zhì)和性能。最終,“凌志”問世,成為當時美國市場上最暢銷的豪華車。
通過這個例子我們發(fā)現(xiàn),不一樣的客戶對產(chǎn)品的價值期望是不同的,過去那種一味地追求高品質(zhì)、經(jīng)濟省油的思維也許并不適合另一人群。只有創(chuàng)造出客戶認為最有價值的產(chǎn)品,才是真正實現(xiàn)了企業(yè)的價值創(chuàng)造。
而在這個過程中,車間是客戶價值需求的直接創(chuàng)造者。他們需要抓住客戶需求,將客戶需求從無形轉(zhuǎn)變?yōu)橛行?。在這里,所有人都應記住一個精益價值理念:下一環(huán)節(jié)即客戶。這句話有兩層含義,一是我們的一切工作或活動都應該由客戶需求來驅(qū)動,二是下一環(huán)節(jié)也是上一環(huán)節(jié)的客戶。
二、精益思想的產(chǎn)生
日本企業(yè)車間里的精益實踐雖然取得了成功,但是這些實踐經(jīng)驗在很長一段時間內(nèi)卻僅僅是被應用于日本國內(nèi),而未得到外界的重視。直至20世紀80年代,日本在制造業(yè)市場上的勝利使美國的制造業(yè)陷于危機,困惑的美國人才開始研究日本生產(chǎn)方面的經(jīng)驗。自此,精益管理得到進一步完善和推廣。
麻省理工學院教授詹姆斯沃麥克、丹尼爾瓊斯等人組織了世界上14個國家的專家、學者,花費了5年時間、耗資500萬元,探索大量生產(chǎn)方式與豐田生產(chǎn)方式的差別。后來,美國麻省理工學院的教授專家們在1990年出版了論述精益生產(chǎn)的經(jīng)典著作《改變世界的機器》,正式提出了“精益生產(chǎn)”的概念,使這種管理方式受到全世界制造業(yè)的關注和推廣。
1980年,美國福特汽車的亨利福特退休,考德維爾和彼得森決定大力引進精益生產(chǎn)方式。他們在工廠的生產(chǎn)線上安裝了停止按鈕,任何工人一旦發(fā)現(xiàn)自己收到的或即將送到下一道工序的產(chǎn)品存在質(zhì)量問題時,就即刻停止生產(chǎn)線。至1987年,福特汽車的盈利超過所有歐洲和日本汽車利潤的總和。
克萊斯勒汽車公司在推行”精益生產(chǎn)”的過程中,也取得了極為可觀的成果。1994年,開發(fā)研制生產(chǎn)新車型所需時間從80年代的60個月縮短到31個月,縮短周期接近-半;新產(chǎn)品開發(fā)人員數(shù)量也縮減了一半;開發(fā)費用大大降低,僅為福特公司同類車型的16;產(chǎn)品的生產(chǎn)周期縮短到原來的3/5,同時產(chǎn)品質(zhì)量有了較大提高。美國汽車公司的經(jīng)驗表明,徹底打破傳統(tǒng)的生產(chǎn)流水線和金字塔式的管理模式,在車間里推行“精益生產(chǎn)”方式,不失為企業(yè)走出困境的一個良策。
就這樣,美國企業(yè)車間開始進行甚至超出日本車間里的精益實踐。專家們認真研究豐田生產(chǎn)方式,并結(jié)合美國企業(yè)的實際情況,將豐田生產(chǎn)方式改造為“精益制造”或“精益生產(chǎn)與管理”。一些企業(yè)甚至將精益生產(chǎn)方式與本公司實際相結(jié)合,創(chuàng)造出了適合本企業(yè)需要的管理體系,例如,1999年美國聯(lián)合技術(shù)公司的ACE管理、精益六西格瑪管理,1998年通用汽車的競爭制造系統(tǒng)等。
此外,美國還開始在很多重要工業(yè)領域推廣精益制造。1993年,美國軍方提出“精益航空計劃LAI”,開展政府指令性的活動,并在波音、洛克希德馬丁等軍工企業(yè)內(nèi)開始推行精益活動。
美國波音公司自實施精益制造管理模式后,波音737飛機總裝時間被縮短到11天。波音公司將推行精益制造的737車間,分為兩班工人24小時工作,通過流動生產(chǎn)和移動作業(yè)等方式總裝飛機,各種飛機零部件都被有條不紊地布排在生產(chǎn)線旁邊。
在737生產(chǎn)間高處的柱子上,設有三蓋與安全、質(zhì)量相關的信號燈,分別是綠燈、黃燈和紫燈。當綠燈亮時,表示一切正常;當黃燈亮時,代表有一些問題,要技術(shù)人員在15分鐘內(nèi)解決問題;當紫燈亮時,表示出現(xiàn)了嚴重問題,所有生產(chǎn)線都需要停止運作,相關技術(shù)工程師要迅速趕到現(xiàn)場,盡快解決問題。
如果說日本豐田汽車公司在車間里的初次探索是精益管理思想的起源,那么美國企業(yè)在車間里的進一步研究則是對精益管理思想的發(fā)展和完善,而這個過程本身也是一種精益思想的體現(xiàn)。然而不論是精益思想本身,還是對精益思想的精益管理,其不斷改善的核心思想都是值得我們每個企業(yè)管理者,特別是車間主管們應該學習的。
建立生產(chǎn)有序、管理順暢,操作規(guī)范,士氣高昂、高質(zhì)量、低成本、短交期的作業(yè)現(xiàn)場;
為企業(yè)規(guī)劃設計一套由內(nèi)到外的形象升級,外觀視覺價值體現(xiàn)、內(nèi)在的管理內(nèi)涵體現(xiàn);
全員參與設備管理高產(chǎn)出和低成本運營,提升設備管理能力,維護能力,提高效率
構(gòu)建班組生產(chǎn)管理體系、循環(huán)評價、人才育成、持續(xù)改善、績效管理、文化養(yǎng)成體系;
提高產(chǎn)品質(zhì)量、降低生產(chǎn)成本、縮短交期、增加利潤,讓管理更系統(tǒng)科學,執(zhí)行力更強
對工廠的各個組成部分進行合理安排,以提高生產(chǎn)效率、降低成本、優(yōu)化物流、改善工作環(huán)境等