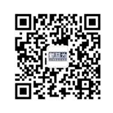
微信公眾號(hào)二維碼
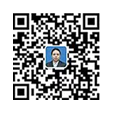
微信咨詢顧問二維碼
新益為TPM咨詢公司概述:設(shè)備維護(hù)管理一直是各大企業(yè)的一個(gè)心病,TPM管理體系在中國(guó)的傳播無疑是一陣春風(fēng),吹到了各大企業(yè)的心坎里,但興奮的同時(shí)也有許多擔(dān)憂,畢竟實(shí)踐才能出真知,具體如何行之有效的推行才是令人頭疼的。
TPM自主維護(hù)
隨著設(shè)備技術(shù)水平的進(jìn)步,設(shè)備的精密程度和復(fù)雜性不斷提高,這對(duì)于設(shè)備實(shí)現(xiàn)安、穩(wěn)、長(zhǎng)、滿、優(yōu)的運(yùn)行提出了更高的要求。逐漸形成了生產(chǎn)部門的操作人員負(fù)責(zé)設(shè)備生產(chǎn)過程的操作和簡(jiǎn)單維護(hù),設(shè)備管理部門的維修人員負(fù)責(zé)設(shè)備狀態(tài)管理和故障排除的局面。
由于體制和分配機(jī)制的原因,很多企業(yè)的操作員工關(guān)注的只是生產(chǎn)計(jì)劃的能否按時(shí)完成或超額完成,經(jīng)常使設(shè)備處于超負(fù)荷運(yùn)行的狀態(tài),設(shè)備常常出現(xiàn)人為操作不當(dāng)和維護(hù)不周導(dǎo)致的故障停機(jī);而設(shè)備維修人員長(zhǎng)時(shí)間忙于設(shè)備停機(jī)后的故障排除和生產(chǎn)恢復(fù),就像一個(gè)救火隊(duì)員,沒有更多的時(shí)間和精力來研究適宜的維修策略和編制針對(duì)性強(qiáng)的維修計(jì)劃。
由于設(shè)備操作人員不對(duì)設(shè)備的狀態(tài)好壞負(fù)責(zé),盡管他們天天使用設(shè)備,了解設(shè)備的日常信息和狀況,但是不能很好地將相關(guān)信息準(zhǔn)確、及時(shí)地傳遞給設(shè)備維修人員。設(shè)備維修人員雖然具備良好的專業(yè)技能和維修經(jīng)驗(yàn),但由于并非天天接觸設(shè)備,加上一些專業(yè)維修隊(duì)伍常常負(fù)責(zé)企業(yè)內(nèi)眾多的設(shè)備維修工作,因此他們不能夠及時(shí)、準(zhǔn)確、完整的獲得他們維修所需要的設(shè)備日常狀態(tài)變化的信息。
此時(shí)設(shè)備狀態(tài)信息的準(zhǔn)確傳達(dá)出現(xiàn)了隔絕,常常導(dǎo)致設(shè)備異?;蚬收蠁栴}不能及時(shí)有效地排除。為了提高設(shè)備的運(yùn)行效率,降低設(shè)備的故障,減少設(shè)備的維修時(shí)間和維修成本,在設(shè)備的維護(hù)保養(yǎng)過程中建立起三道保護(hù)屏障是非常必要的。
1、TPM自主維護(hù)管理中建立的第一道保護(hù)屏障在設(shè)備維護(hù)保養(yǎng)過程中,建立起以操作員工為主的TPM自主維護(hù)管理閉環(huán),這是設(shè)備維護(hù)保養(yǎng)的第一道保護(hù)屏障。TPM自主維護(hù)管理首先從操作員工的設(shè)備清掃開始,清掃本身同時(shí)也是對(duì)設(shè)備關(guān)鍵點(diǎn)進(jìn)行檢查的過程,并隨時(shí)做好檢查記錄,然后對(duì)設(shè)備進(jìn)行力所能及的基本保養(yǎng),內(nèi)容包含緊固、潤(rùn)滑、調(diào)整、更換、堵漏、防腐等環(huán)節(jié);然后又回到最初的清掃環(huán)節(jié)。
2、專業(yè)維修設(shè)備維護(hù)保養(yǎng)過程中建立的第二道保護(hù)屏障設(shè)備操作運(yùn)行人員在第一道保護(hù)屏障所建立起來的TPM自主維護(hù)管理過程中,如果發(fā)現(xiàn)設(shè)備存在異常染源頭、一些很難進(jìn)行清掃的部位、一些造成故問題或隱患,同時(shí)由于受專業(yè)技術(shù)知識(shí)和維修條障的潛在因素、生產(chǎn)現(xiàn)場(chǎng)的各種浪費(fèi)、影響產(chǎn)品件的限制以及制度規(guī)范的約束自己無法解決,則質(zhì)量的生產(chǎn)和加工環(huán)節(jié)以及潛在的事故發(fā)生源,通過向?qū)I(yè)維修部門遞交設(shè)備故障維修單的方式我們把這些歸納為六源。
在這個(gè)過程中,企業(yè)要跳出TPM自主維護(hù)管理閉環(huán),進(jìn)入專業(yè)維修閉環(huán),由專業(yè)引導(dǎo)員工去發(fā)現(xiàn)并解決這些源頭,并與生產(chǎn)現(xiàn)場(chǎng)維修人員對(duì)設(shè)各進(jìn)行診斷維修,維修結(jié)束又回到的持續(xù)改善、難題攻關(guān)及合理化建議活動(dòng)融為一正常的TPM自主維護(hù)管理閉環(huán),這是通過設(shè)備維護(hù)保養(yǎng)建體,形成現(xiàn)場(chǎng)改善和進(jìn)步的強(qiáng)大助推力。
通過這立起的第二道保護(hù)屏障。些改善和改進(jìn)活動(dòng),使生產(chǎn)效率得以提升,員工技能也能得到全面提高,并逐步具各發(fā)現(xiàn)設(shè)備異
3、維修預(yù)防設(shè)備維護(hù)保養(yǎng)過程中建立的第三道保常、會(huì)處理小問題、會(huì)改善的能力。護(hù)屏障有些企業(yè)會(huì)有這樣的一些顧慮,操作員工去預(yù)防維修閉環(huán),這是通過設(shè)備維護(hù)保養(yǎng)建立修設(shè)備,那維修人員做什么?操作人員去修設(shè)備,起的第三道保護(hù)屏障。對(duì)于專業(yè)維修人員在判斷那修壞了怎么辦?這里反映了企業(yè)存在的一個(gè)誤故障時(shí)發(fā)現(xiàn)的共性問題,企業(yè)需要組織開展“他區(qū),那就是維護(hù)=維修。事實(shí)上,維護(hù)并不等于維機(jī)類比點(diǎn)檢”。
所謂他機(jī)類比點(diǎn)檢,就是將某臺(tái)修。操作員工參與TPM自主維護(hù)管理是在規(guī)定的范圍內(nèi)按設(shè)備出現(xiàn)過的故障或隱患等,有計(jì)劃的安排對(duì)其規(guī)范對(duì)設(shè)備進(jìn)行必要的保養(yǎng)活動(dòng),從而使維修人他同類設(shè)備或部位進(jìn)行專項(xiàng)檢查,評(píng)估其是否也員可以擺脫那種疲于應(yīng)付設(shè)備異常和故障的狀存在類似的現(xiàn)象。
TPM自主維護(hù)管理是TPM設(shè)備管理中八大支柱之一,是設(shè)備維護(hù)的一大利器,但是他需要員工有高度的自覺性和素養(yǎng),強(qiáng)調(diào)自己的機(jī)器自己維護(hù),既人人都是設(shè)備維修人員,所以要實(shí)施這一體系少不了對(duì)員工意識(shí)的培訓(xùn)。
建立生產(chǎn)有序、管理順暢,操作規(guī)范,士氣高昂、高質(zhì)量、低成本、短交期的作業(yè)現(xiàn)場(chǎng);
為企業(yè)規(guī)劃設(shè)計(jì)一套由內(nèi)到外的形象升級(jí),外觀視覺價(jià)值體現(xiàn)、內(nèi)在的管理內(nèi)涵體現(xiàn);
全員參與設(shè)備管理高產(chǎn)出和低成本運(yùn)營(yíng),提升設(shè)備管理能力,維護(hù)能力,提高效率
構(gòu)建班組生產(chǎn)管理體系、循環(huán)評(píng)價(jià)、人才育成、持續(xù)改善、績(jī)效管理、文化養(yǎng)成體系;
提高產(chǎn)品質(zhì)量、降低生產(chǎn)成本、縮短交期、增加利潤(rùn),讓管理更系統(tǒng)科學(xué),執(zhí)行力更強(qiáng)
對(duì)工廠的各個(gè)組成部分進(jìn)行合理安排,以提高生產(chǎn)效率、降低成本、優(yōu)化物流、改善工作環(huán)境等